Hayashi Sangyo Co.,Ltd.
Production Process
- Introduction to the Manufacturing Process of Polyethylene Packaging Materials
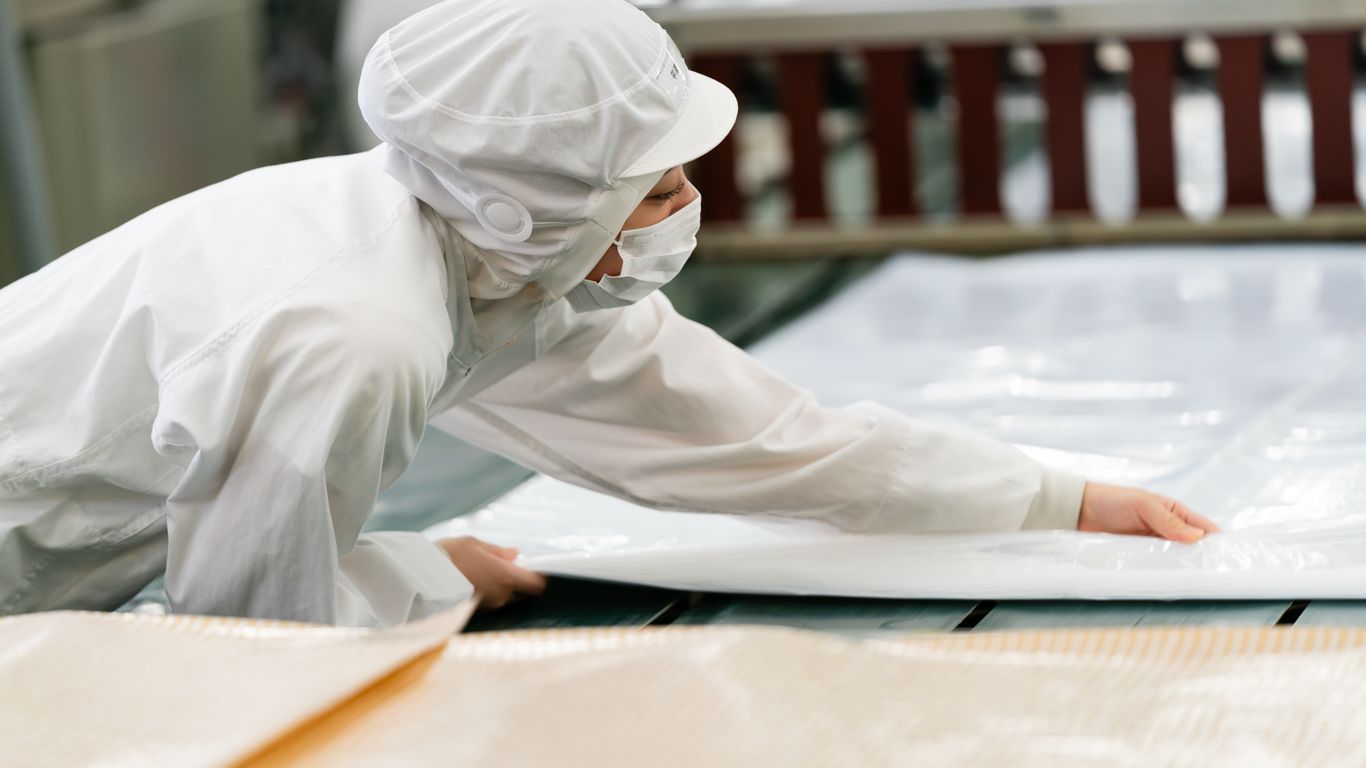
- Home
- Production Process
Production Process
BLOWN FILM EXTRUSION
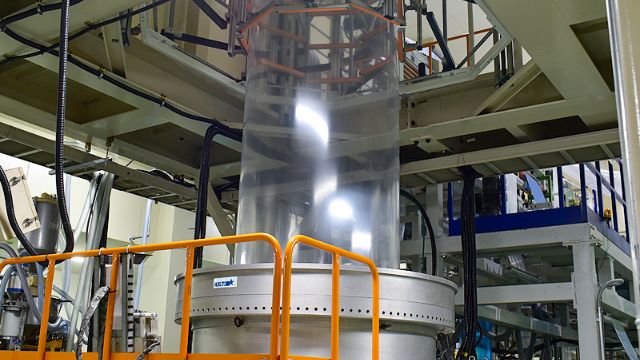
We heat and melt pelletized polyethylene raw material, shaping it into a cylindrical form. Air is blown in, inflating it like a balloon while cooling simultaneously. The material is then folded into two layers between two plates and wound using a winding machine.
Various blown film machines in our plant can meet your diverse size requirements. Our blown film lines are capable of lay-flat tube width up to 3200mm.
PRINTING
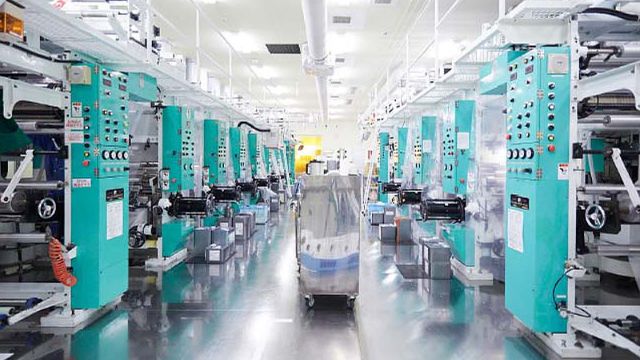
This process uses engraved plates to print on films created through the blown film extrusion process. Ink is applied to the engraved plate, excess ink is removed with a blade, and the ink is then transferred to the film between the plates using a roller and the gravure printing method. In our printing facility, we have three sets of gravure printing machines that can handle 1 to 7 colors.
BAG MAKING
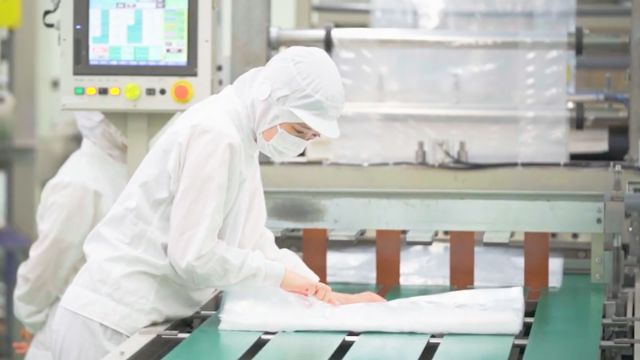
Heat sealing is a process of sealing one thermoplastic material to another thermoplastic material with heat and pressure.
The tube film will be closed by heat sealing process and then cut into individual bags in this process.
Our bag making lines are capable of producing big-size flat bags,square bottom bags or other shapes of bags with maximum width of 2,000mm.
Production Capacity of Domestic Factories
Blown Film Extrusion
Mito Plant
LDPE / LLDPE / Blown Film Lines
Size | (lay-flat width) max.3000mm (4 multi-layer machines) |
---|---|
Capacity | 4,000 tons per year (13 machines) |
Manufacturing Environment | Mito No.1 Plant :positive pressure air cleaning system,door interlocking system Mito No.2 Plant :positive pressure air cleaning system,door interlocking system |
Hitachinaka CMP Plant
LDPE / LLDPE / Blown Film Lines
Size | (lay-flat width:)max.3,200mm (3 multi-layer machines) |
---|---|
Capacity | 6,000 tons per year (17 machines) |
Manufacturing Environment | Blown Film CMP No.1 Plant : positive pressure air cleaning system, door interlocking system,NASA class 100,000 Blown Film CMP No.2 Plant 2: positive pressure air cleaning system, door interlocking system,NASA class 100,000 |
Printing
Hitachinaka CMP Plant
Printing Method | rotogravure printing |
---|---|
Printing Machine | 1 senven-color printing machine,1 three-color printing machine |
Printing Size | width: max.700mm / printing pitch: max.900mm |
Capacity | 30 million meters |
Manufacturing Environment | positive pressure air cleaning system,door interlocking system,NASA Class 100,000 |
Bag Making
Mito Plant
Product | flat bag / gusset bag / pallet cover ECOTEX&ECOTEX2 |
---|---|
Bag Making Size | width: 200 〜 2,000 mm |
Manufacturing Environment | positive pressure air cleaning system/door interlocking system/NA class 10000 |
Capability | 1,500 tons per year |
Hitachinaka CMP Plant
Product | flat bag / gusset bag pallet cover ECOTEX |
---|---|
Bag Making Size | width: 200 〜 2,000 mm |
Manufacturing Environment | positive pressure air cleaning system/door interlocking system/NA class 100,000 |
Capability | 4,500 tons per year |